For many decades KHIMIK has been a leading manufacturer and developer of the specialized products which provide solutions to critical resource-saving tasks for industrial enterprises and industries, such as oil and gas complex, construction, automobile industry.
The products created by our company allow to extend the service life of expensive structures, parts, materials, improve the quality of repair and preventive maintenance at industrial facilities, provide increased reliability of mechanisms and structures during operation in severe weather and climate conditions.
Fundamental experience and knowledge of scientists and developers from the KHIMIK Engineering Center and Testing Laboratory, continuous search for new technological solutions and enhanced cooperation with world's leading experts in various fields of applied chemistry allow us to offer the market really relevant and at times unique products meeting the most stringent requirements of our customers.
Our research and production capacity allows us to find solutions to the tasks of any complexity, which determines the innovative nature of our activities. This factor is particularly valuable from the point of view of our regular customers, specialized enterprises for which we create individual products with special properties and characteristics.
We are proud of the long-standing partnerships and collaborations with our customers and look forward to remaining a reliable supplier for them in strategic perspective. A critical task for the company has been and remains the development and creation of products that are safe in terms of their use, production and further environmental impact. This aspect is given special attention within the framework of the Quality Policy adopted by the company.
Oil & Gas
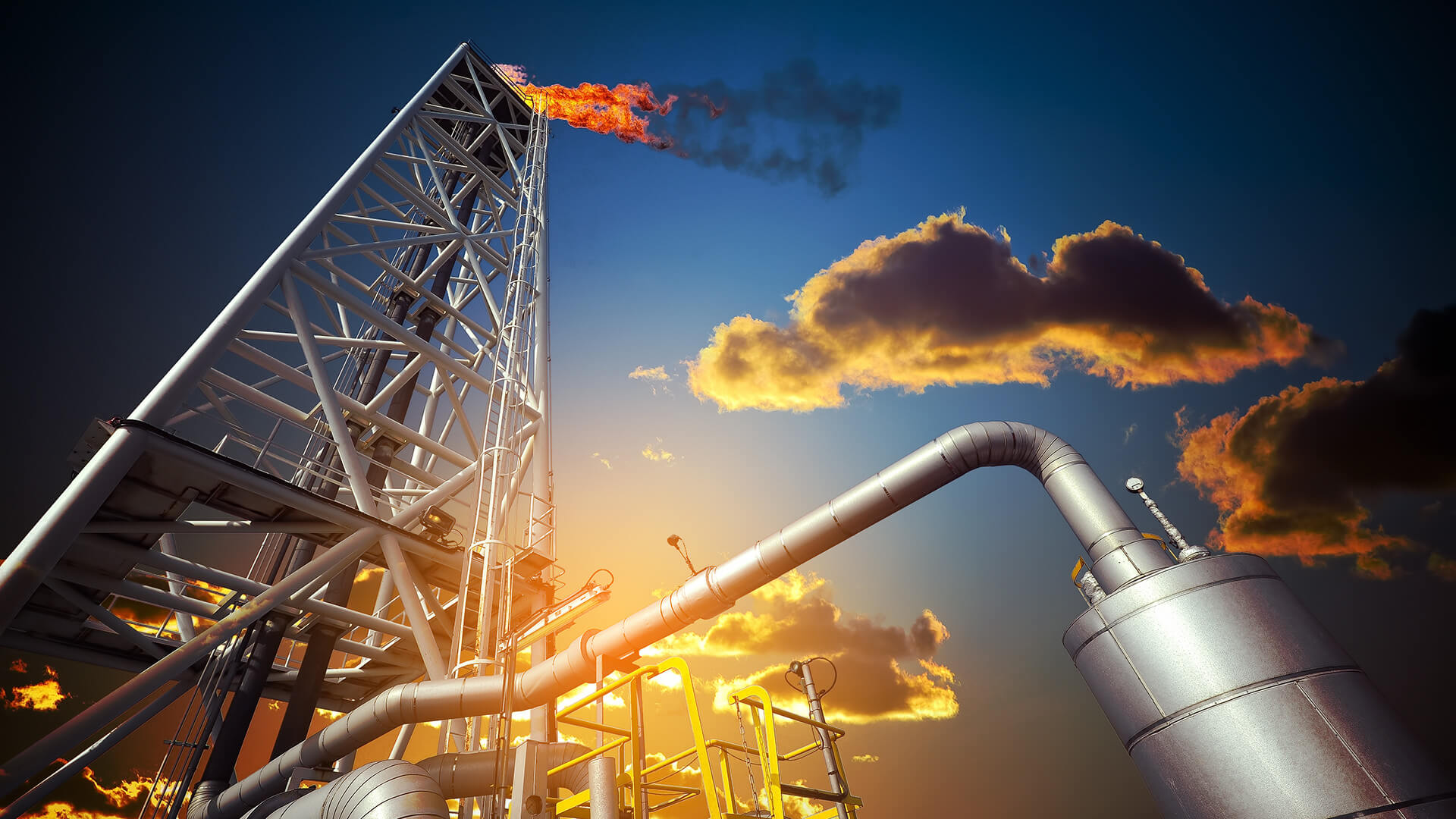
- Internal smooth (antifriction) pipe coatings
- Pipeline corrosion protection
- Paintwork materials for tanks with oil products
- Materials for auxiliary operations
One of the priority areas of the company's activity is creation of materials for anticorrosion protection of oil-and-gas production equipment: pipelines, shaped elements, shut-off valves, vessels for oil products storage, metal structures of various applications.
The complexity of the task is specified by the high corrosiveness of the environment in which the equipment is operated. Crude oil and the formation water emulsified in it contain dissolved salts, carbon dioxide and hydrogen sulphide. The most dangerous is the hydrogen-sulphide corrosion, which even corrosion-resistant grades of steel cannot resist. Additional negative factors reduce the service life of pipelines, including: periodic and constant mechanical loads, higher temperature, high abrasivity of environment, hardness deposition and asphaltene-resin-paraffin deposits (ARPD), and the use of various chemical reagents for pipe cleaning. The tubing and in-field pipelines are operated under the most severe conditions.
The multifactorial nature of the task and considerable differences in the composition of the corrosive medium in different fields complicate the creation of the paintwork material which provides reliable corrosion protection. When creating materials that can withstand the corrosive medium for a long period, we take into account the complete range of conditions effecting the coating service life. It includes the operating conditions of a coating such as the chemical composition of the medium, temperature and pressure, mechanical stress, and climatic conditions at a given location. Coating conditions: methods and quality of surface preparation, used equipment, modes of application and curing, as well as methods of transportation and storage conditions of finished products.
Developed materials are thoroughly tested for compliance with the requirements of regulatory documentation. The whole range of tests is carried out: physical and chemical, climatic, confirming the compliance of the declared properties of the material and coating with the actual ones. Tests are carried out during the development process using the in-house equipment, and then in industry institutes that authorize the use of materials by specific customers.
The used technologies enable to adapt a number of technological characteristics, such as rheological properties, curing time, to the process equipment of coating plants.
When developing paintwork materials for industrial use, we strived to minimize labor costs during their application. For this purpose the paintwork materials have been developed which allow to apply the coating of required thickness in a single layer. Rheological properties of these materials allow to obtain coatings up to 800 µm thick on vertical surfaces, and high anti-corrosion properties, chemical resistance and excellent adhesion provide long service life and performance characteristics of the coating.
1.1. Pipeline corrosion protection
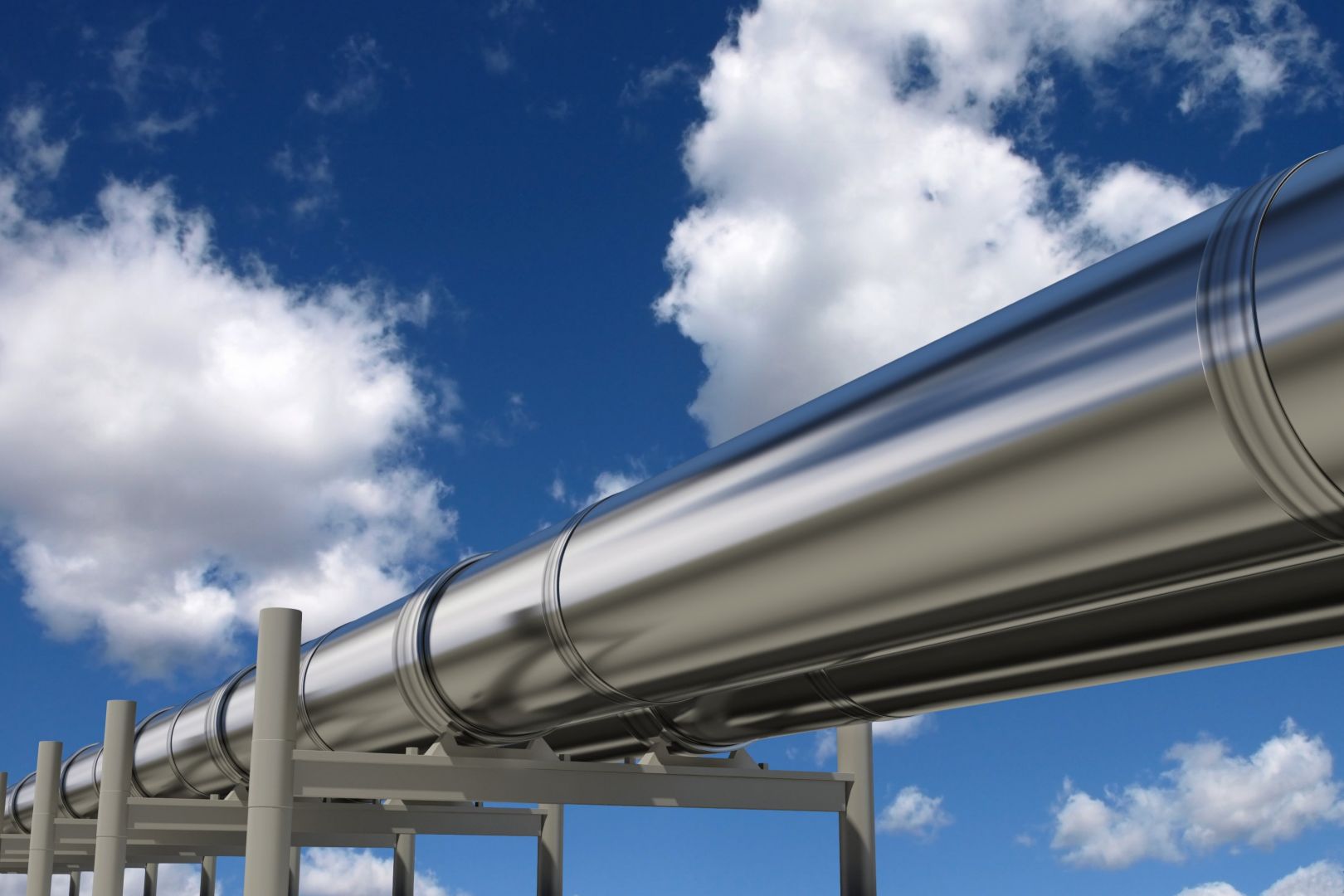
One of the main reasons for high accident rate of in-field oil pipelines is corrosion caused by the joint action of corrosive medium and mechanical loads. Corrosion damage causes up to 30% of pipeline failures. In this regard, it becomes impossible to ensure safe operation of the pipeline systems and increase their service life without addressing the issues of corrosion protection of the outer and inner surfaces of pipes and welded joints.
One of the methods of the pipeline corrosion protection is insulation of metal surface against the corrosive medium by polymer coatings, including the paint ones. The applied paintwork materials should be very resistant to the pumped medium at temperatures and pressures of pipeline operation, and technologically simple when applied and transported. As a rule, two-component thixotropic materials are used, enabling to get a coating of the required thickness in one pass.
Materials for corrosion protection of pipeline transport:
- Pipeline corrosion protection. Outer surface
- Pipeline corrosion protection. Inner surface
Pipelines: Inner surface
Two-component enamels TREPP-TR, TREPP-TR-90
Designed for anticorrosion protection of the inner surface of steel pipes transporting oil, water-oil-gas mixtures, oil products, sea and industrial water, cold and hot. The enamels are resistant to cathodic disbondment and can therefore be applied together with cathodic protection for pipelines, and are also highly abrasion-resistant. TREPP-TR-90 enamel can be used at temperatures up to 90 °C, has a permit for contact with drinking water. TREPP-TR enamel can be used at temperatures up to 60 °C. It is recommended for internal anticorrosion coating of tubing. The service life of the coatings reaches 10 years.
Powder coating primer TREPP-GP-2
This is an epoxyphenol primer designed to form an adhesive layer on metal prior to applying powder coatings onto the internal surface of pipelines. It improves the anticorrosive properties and adhesion of a surface.
These are used for the internal protection of main gas pipelines. The materials create an antifriction (smooth) layer that reduces the gas dynamic impedance of the gas pipeline and energy expenditure for gas pumping. They also provide corrosion protection in the time between the fabrication and installation of a pipeline. The TREPP-TRG-1 enamel contains no solvents at all, and the TREPP-TRG-2 enamel has a low solvent content.
Pipelines: Outer surface
Two-component polyurethane enamel Ritan-531
Used for external corrosion protection of undersurface pipelines, fittings, and stop valves. Fast-curing. Rheological characteristics allow it to be applied onto vertical surfaces, with a coat of up to 3 mm. The coating has high anticorrosive properties, resistance to water and cathodic polarization, adhesion and impact strength, and also high tensile strength.
One-component hot-curing primer TREPP-GO-1
It is designed to improve adhesion and enhance the protective properties of external polymer coating of pipelines. It is used in industrial lines of extrusion applying of a protective coating which consists of an ethylene vinyl acetate copolymer layer and a polyethylene layer, wherein it is the first layer before the copolymer layer. It is applied immediately before extruding the protective polymer coating.
Epoxy one-pack enamel TREPP-GO-2
No solvents. The main purpose is anticorrosive wear-resistant coating of driven piles, protection of the outer surface of pipelines before applying polyurethane foam insulation.
1.2. Paintwork materials for tanks with oil products
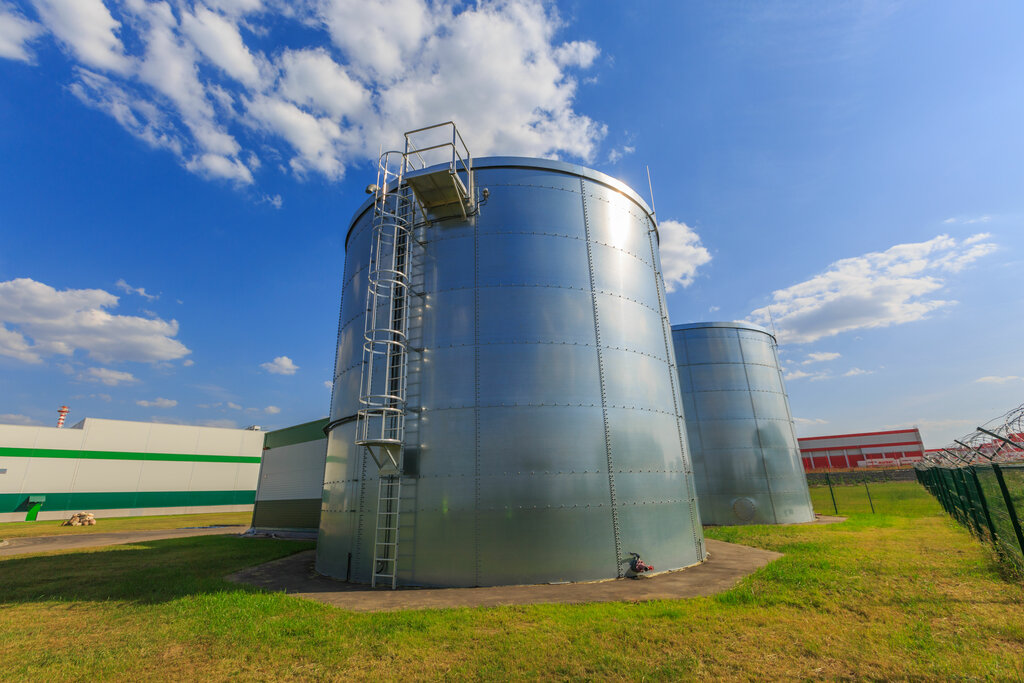
External and internal coating systems have been developed for corrosion protection of tanks for storage of oil products and crude oil containing formation water, hydrogen sulphide and water-soluble salts. Internal coatings are highly resistant to oil products, highly corrosive components of crude oil, synthetic detergents and water vapor used in tank sediment cleaning. High physical-mechanical properties and adhesion of coatings prevent their integrity violation in case of deformation of tank walls and bottom under the hydrostatic pressure and alternating temperature loads.
For corrosion protection of metal structures and external surface of tanks a two-layer coating RITAN has been developed, consisting of one layer of primer enamel TREPP-RV-726N and one layer of enamel RITAN-755.
The first coating layer performs anti-corrosion functions with high barrier properties and a long-lasting passivation effect. The second one, a finish layer of the coating, protects from insolation, humidity, precipitation. The coating can be used in climatic regions according to GOST 16350: I1 (very cold), I2 (cold), II4 (moderately cold) for different atmospheric corrosiveness categories C5-M, C4, C3 (ISO 12944-2 and ISO 9223). The service life of coatings is up to 20 years.
Epoxy two-component primer enamel TREPP-RV-726N
It is applied as the first layer using airless spraying installation. It contains no more than 20% of solvents. Simply mix a quantity of enamel components required for an hour of work prior to use. It provides the coating system with high anti-corrosion and physical-mechanical properties. Recommended layer thickness of TREPP-RV-726N primer enamel depends on the operating conditions and the required service life of the coating.
Finish two-component polyurethane enamel RITAN-755
It is applied by airless spraying installations with preliminary mixing of components. The second layer is in the coating system. Simply mix a quantity of enamel components required for an hour of work prior to use. The enamel is highly UV resistant, glossy and semi-glossy, with reduced dirt retention. It comes in a variety of colors. It contains no more than 35% of solvents. It is applied with a layer thickness of 80–100 µm.
The coating systems based on primer enamel TREPP-RV-726N and enamel RITAN-755, except for painting of steel tanks, are designed for corrosion protection of metal structures, outer surfaces of pipelines and equipment operating in atmospheric conditions.
Tank farm: Inner surface
TREPP-RV-726
Two-component epoxy enamel with low solvent content, amine-type hardener. It is designed for corrosion protection of the inner surface of steel tanks for storage of light and dark oil products, water, oil, condensate, washing fluid, ballast tanks and pipes transporting oil and oil-gas mixtures. It withstands periodic exposure to detergents at 75 °C and water vapor at 100 °C. Operating temperature is from minus 60 °C to plus 90 °C. It is used as a primer layer in the coating system with RITAN-755 enamel during operation in the ambient atmosphere, can be used as an independent coating during operation indoors, underground and in thermal insulation systems for metal corrosion protection.
Surface preparation – abrasive blast cleaning to Sa 2½ degree. The surface roughness (Rz) after cleaning should be between 40 and 80 µm. When equipped with winter hardener, the application temperature can be reduced to minus 10 °C, but the drying time of enamel to degree 3 will increase from 9 hours at 20 °C to 7 days. The application method is airless spraying. Recommended equipment: single-component units capable of providing pressure 120–150 bar.
Two-component epoxy enamels TREPP-RV-726N, TREPP-RV-726SV
These enamels have a high non-volatile content (min. 80%). They are intended to protect the inner surface of tanks. TREPP-RV-726N enamel for anticorrosive coatings of tanks for oil and dark oil products storage. TREPP-RV-726SV enamel for anticorrosive coatings of tanks for storage of light oil products, prevents the formation of static electrical discharges on the inner surface of the tank. They are very durable and can be applied by means of airless spray systems with premixed components. Simply mix a quantity of enamel components required for an hour of work prior to use.
Tank farm: Outer surface
RITAN-755
It is applied by airless spraying installations with preliminary mixing of components. The second layer is in the coating system. Simply mix a quantity of enamel components required for an hour of work prior to use. The enamel is highly UV resistant, glossy and semi-glossy, with reduced dirt retention. It comes in a variety of colors. It contains no more than 35% of solvents. It is applied with a layer thickness of 80–100 µm.
For corrosion protection of metal structures and external surface of tanks a two-layer coating RITAN has been developed, consisting of one layer of primer enamel TREPP-RV-726N and one layer of enamel RITAN-755. The first coating layer performs anti-corrosion functions with high barrier properties and a long-lasting passivation effect. The second one, a finish layer of the coating, protects from insolation, humidity, precipitation. The coating can be used in climatic regions according to GOST 16350: I1 (very cold), I2 (cold), II4 (moderately cold) for different atmospheric corrosiveness categories C5-M, C4, C3 (ISO 12944-2 and ISO 9223). The service life of coatings is up to 20 years.
The coating systems based on primer enamel TREPP-RV-726N and enamel RITAN-755, except for painting of steel tanks, are designed for corrosion protection of metal structures, outer surfaces of pipelines and equipment operating in atmospheric conditions.
Epoxy two-component primer enamel TREPP-RV-726N
It is applied as the first layer using airless spraying installation. It contains no more than 20% of solvents. Simply mix a quantity of enamel components required for an hour of work prior to use. It provides the coating system with high anti-corrosion and physical-mechanical properties. Recommended layer thickness of TREPP-RV-726N primer enamel depends on the operating conditions and the required service life of the coating.
1.4. Materials for auxiliary operations
G-039 (winter)
Used to seal protection sleeves installed in pipes at the welded seam area. Can be used for connecting pipes using the cone-socket method. Two-pack, epoxy-based, with good adhesion to pure metal and epoxy coatings. Produced in summer and winter versions. The winter version of the sealant has a high curing rate at negative air temperatures.
RITAN-41
RITAN-41 solvent is intended for cleaning of paint equipment after application of urethane and epoxyurethane enamels. RITAN-41 solvent is produced according to Specification 2319-126-00205357-2011.
TREPP-KP
Based on trivalent chromium salts, contains no hexavalent chromium salts. Low-toxic. It is intended for treatment of pipe surfaces after shot blasting for two- and three-layer external coating. Creates a dense insoluble chromate film on the steel surface, which increases the anticorrosive properties of the coating system, adhesion strength and resistance to cathodic disbonding. The compound is applied evenly to the pipe surface heated to a temperature of 40–60 °C by any method. After drying to the degree of “dry to the touch”, the treated surface is heated to 130–230 °C until the color changes from pale blue to yellow-golden.
TREPP-OR
Effective agent for removal of oil and fat impurities, residues of process fluids used in the manufacture of pipes, to reduce the content of soluble salts on the metal surface, removal of mechanical impurities. Low consumption and negligible foaming. Application of the agent, in accordance with the technology, does not affect the adhesion of paintwork materials.
TREPP-R-1
TREPP-R-1 solvent is intended for dilution of epoxy and epoxyphenol enamels and cleaning of paint equipment. TREPP-R-1 solvent is produced according to Specification 2319-126-00205357-2011.
TREPP-R-2
TREPP-R-2 solvent is intended for dilution of epoxy and epoxyphenol enamels and cleaning of paint equipment. TREPP-R-2 solvent is produced as per Specification 2319-126-00205357-2011.
TREPP-R-3
TREPP-R-3 solvent is intended for dilution of epoxy and epoxyphenol enamels and cleaning of paint equipment. TREPP-R-3 solvent is produced as per Specification 2319-126-00205357-2011.
Support infrastructure facilities
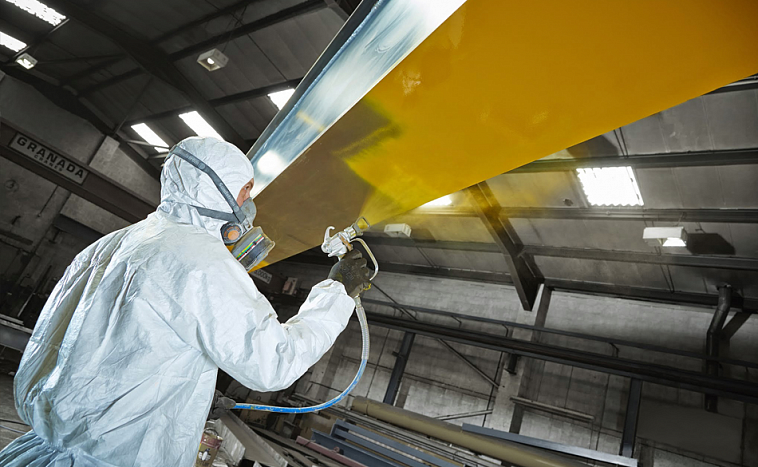
The coating system consisting of one primer layer with thickness of 120 µm and one enamel layer with thickness of 80 microns is designed for service life not less than 10 years in conditions of atmosphere corrosive aggressiveness C4. The materials can be applied at temperatures down to minus 20 °C and are highly weather resistant.
PROFLEX-306
PROFLEX-306 one-component alkyd primer is designed for corrosion protection of metal structures made of carbon, galvanized and stainless steel during operation under ambient atmospheric conditions. Quick drying, can be applied at ambient air temperature down to minus 20 °C, oil-and-petrol resistant. It is intended, among other things, for painting metal structures in plant conditions. After full polymerization it can be overlapped with alkyd, acrylic, polyurethane and other paintwork materials.
PROFLEX-256
One-component finishing enamel for anticorrosive coating systems of metal structures. Coating on its basis has high resistance to solar radiation and other weather factors in a wide range of atmospheric aggressiveness and in various climatic zones. Retains gloss and color throughout use. Quick drying, can be applied at ambient air temperature down to minus 20 °C, oil-and-petrol resistant.
PROFLEX-201
Two-component epoxy primer designed for long-term corrosion protection of metal structures in various climatic conditions. It is used as a primer layer in the coating system with finishing enamels based on acryl and acrylic-urethane on the surfaces made of carbon, galvanized and stainless steel.